My main responsibilities revolved around CADing prototypes for capsules that would assume different geometries to maintain prolonged residence in the GI tract. These capsules would hold the drugs that would diffuse over a controlled time.
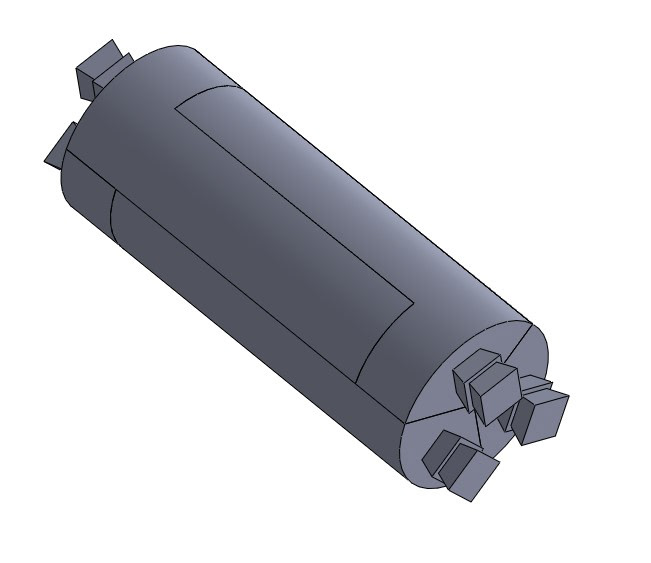
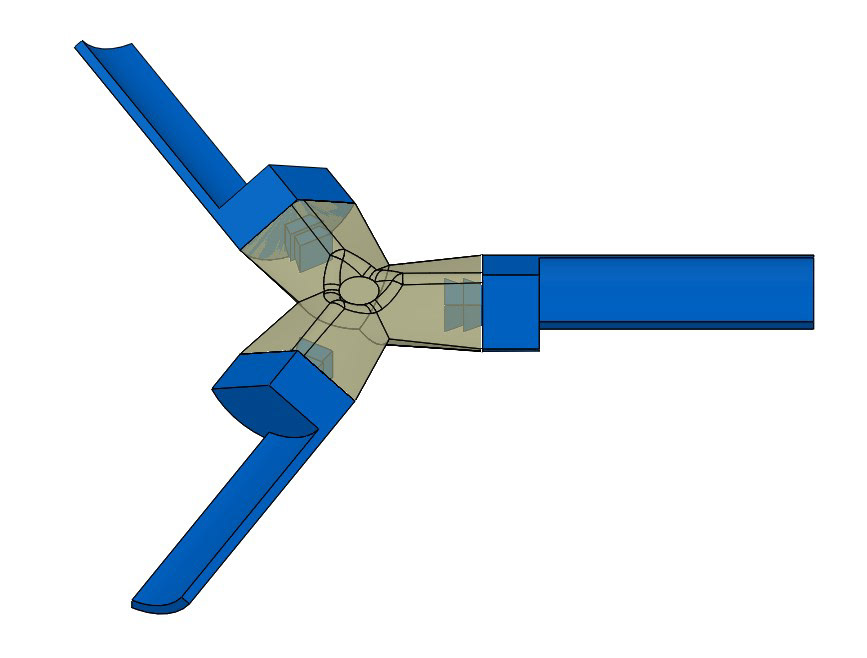
I designed what I call a 3-armed dumbell capsule. The image on the left is its closed geomtetry. The image on the left is one half of its open geometry (one weight of the dumbell). The cores would be connected by a thin rod (dumbell bar) to achieve dumbell shape. The idea behind this design was that if one arms were to break, the device would still be in a configuration that wouldn't allow it to pass through the pylorus until it was supposed to.
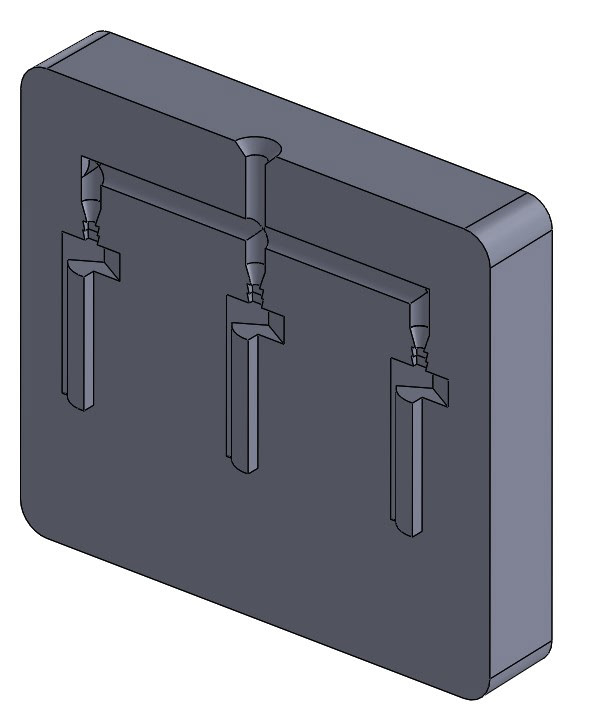
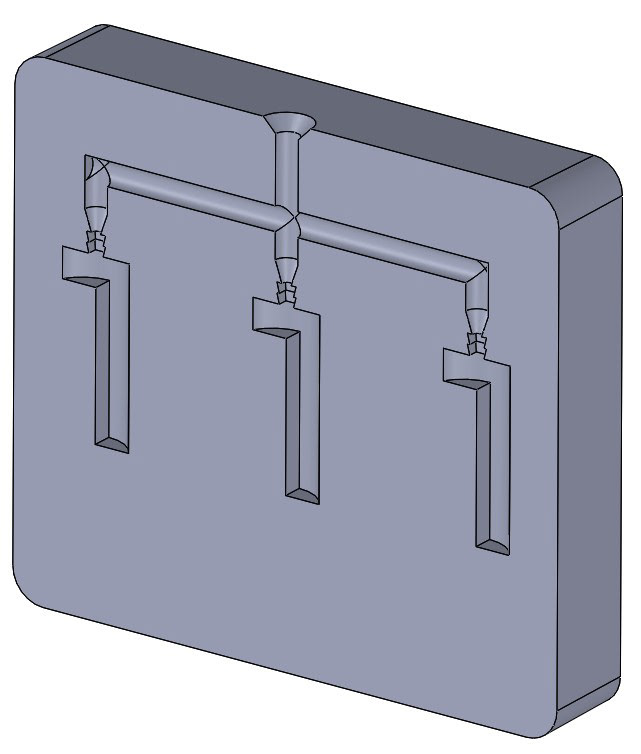
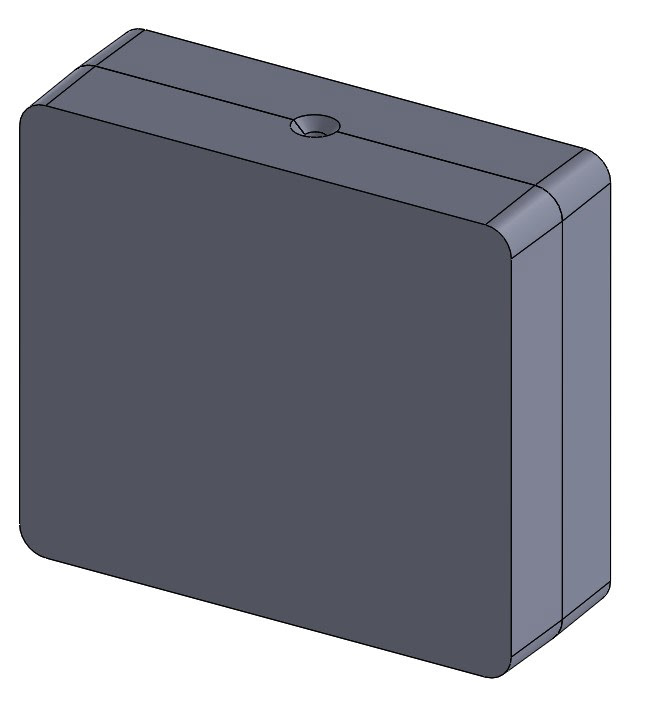
The prototypes for this design and many others were made with injection molding. I learned how to design molds for my arms and operate an injection molding machine. I tested several different polymers with different melting and hardening temperatures and evaluated their biocompatibility, elasticity, strength, and overall compatibility with each specific design.
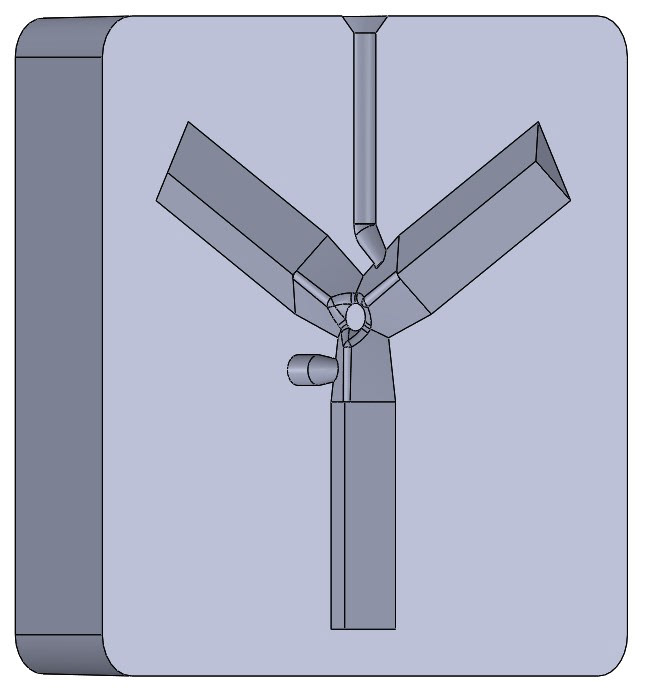
The final step of fabrication was to place the arms in the full assembly mold and injection mold to core to connect the full device. The polymers I chose for both the arms and core were different (since the parts would experience different forces), but were compatible so that they chemically fused to make a robust structure that couldn't easily separate.
I also performed INSTRON tests on the different capsule configuarations to evaluate their structural integrity under the loads they would experience in the GI tract.