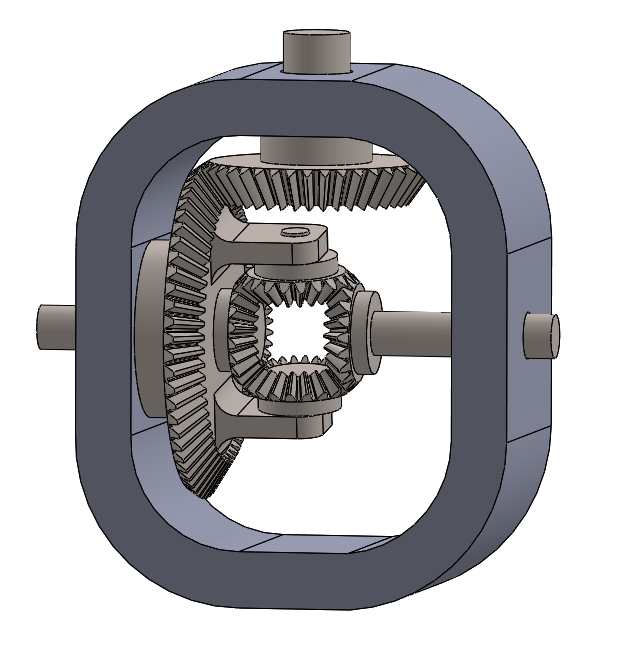
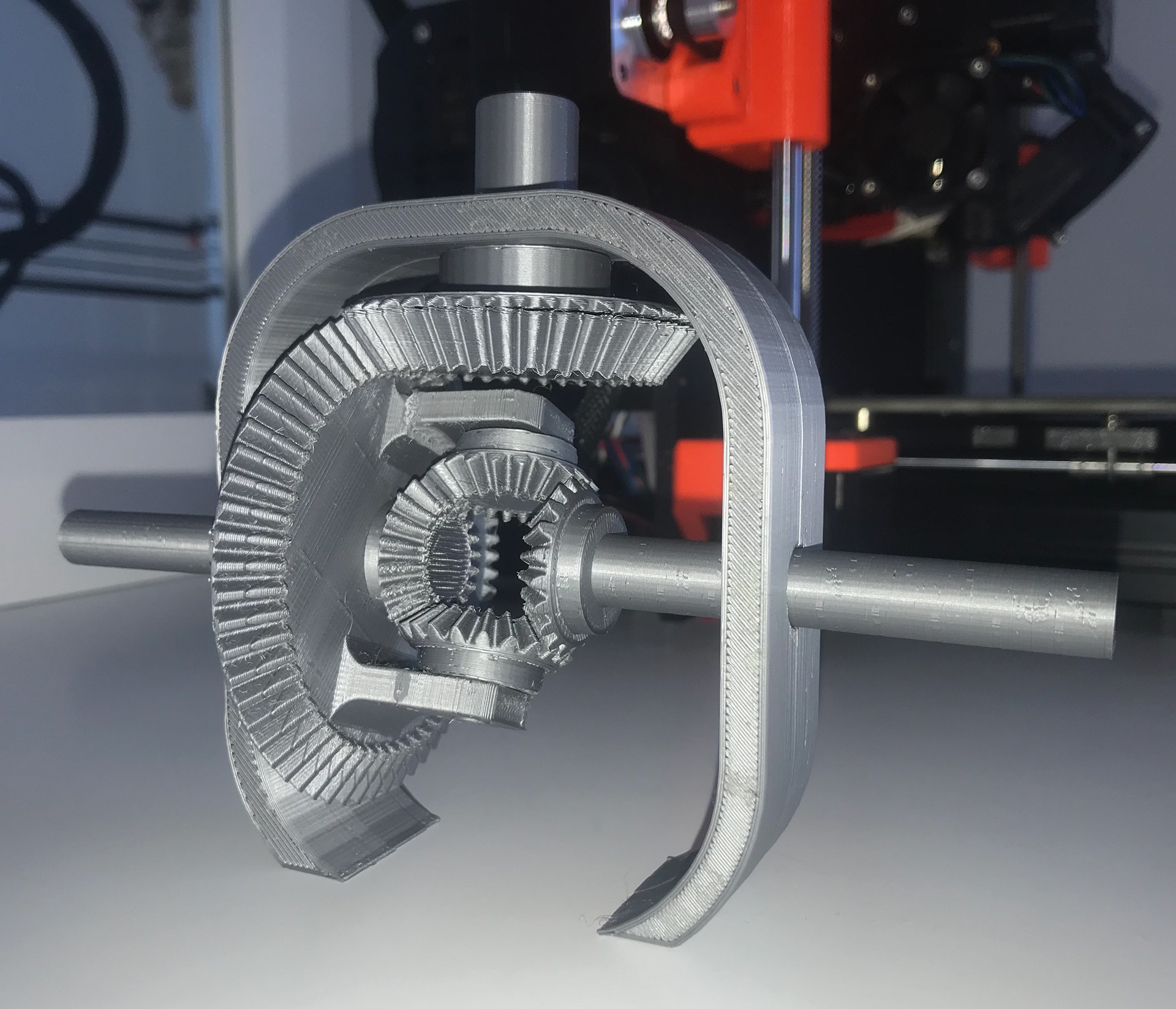
Of course, each part of the assembly had to be printed separately:
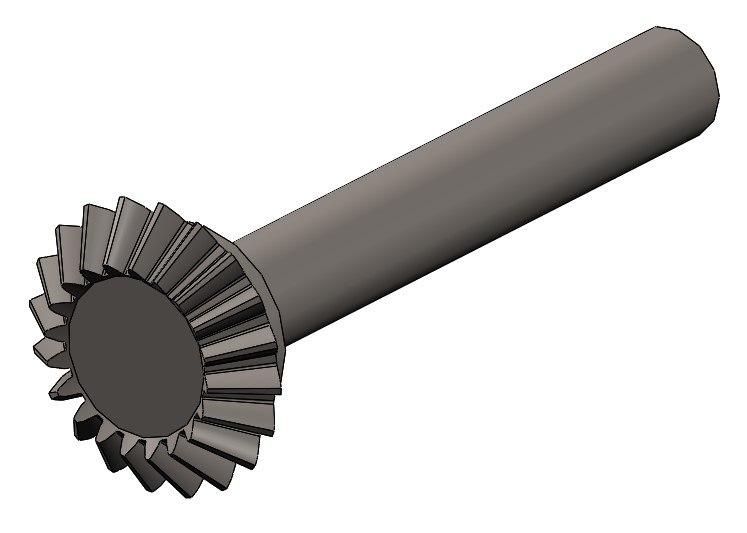
Side Axle Gear
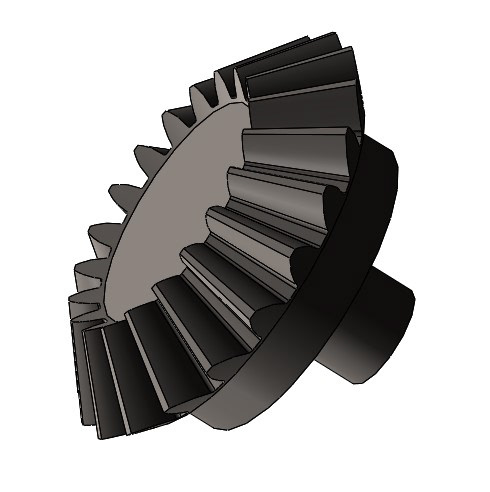
Spider Gear
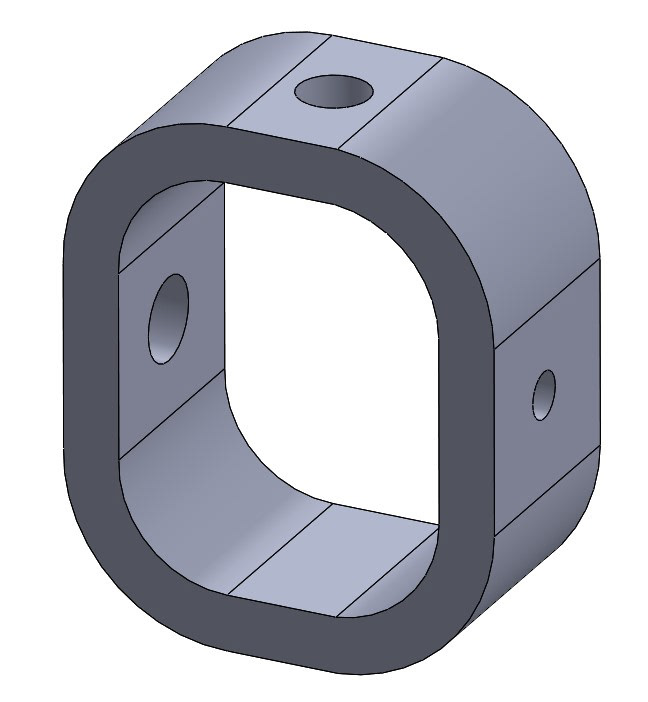
Gear Box
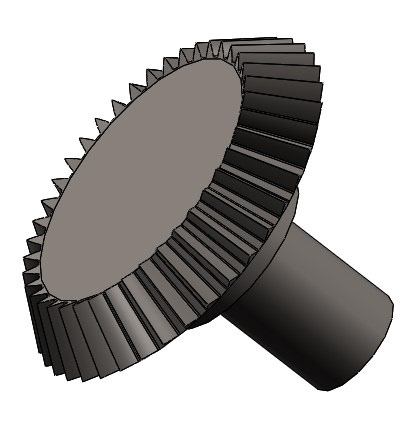
Pinion Gear
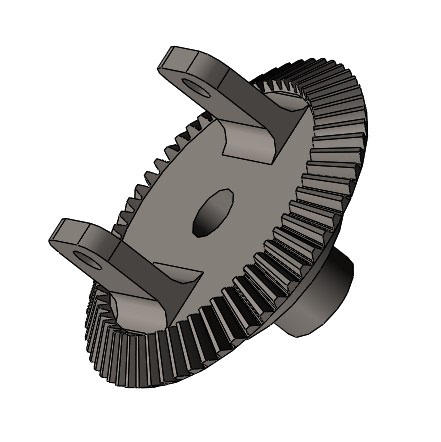
Ring Gear
This taught me first hand about designing while taking into account tolerances and fit. While my parts may have fit perfectly together in the SolidWorks assembly, they were too tight when I first attempted to assemble them in real life. I forgot to take this into account when dimensioning for printing and had to redesign the parts and their holes.
I also had to think about order of assembly and how I was going to merge all the gears together within their box. As you may be able to see, I had to break and reattach the spider gear mounts so that they would properly interlock with the axle gears. I also split the gear box so I could sandwich the axles in place.
The design could obviously be smoother and I would love to make wheels for this guy. Right now, I'd call this a work in progress. I want to improve on this project by designing a cooler gear box, simulating the motion in SolidWorks, making a cage for the gears, and maybe messing around to make a slip differential????